Concrete pump fails are inevitable in the daily use and maintenance of concrete pumping equipment process. In order to apply the concrete pumping equipment more efficiently, mastering the common equipment problems and their handling methods is necessary.
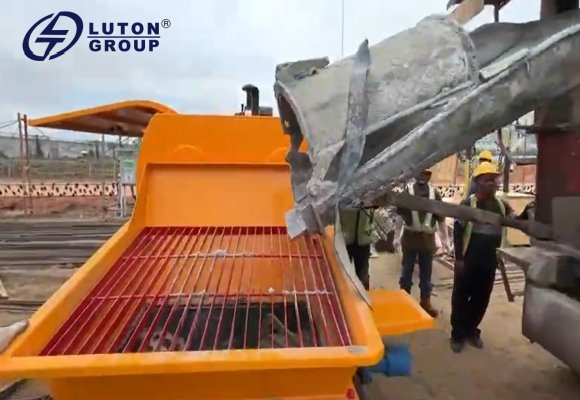
Main Concrete Pump Fails
Main concrete pump fails in common use include: pipe blockage or slurry leakage, insufficient pressure or no pressure, electrical failure, mechanical failure, etc. The causes of these problems are various, but most of them are avoidable.
The Pipe Blockage And The Slurry Leakage
In the concrete pumping process, sometimes, the concrete can not pass through the pipeline or the slurry leaks through the pipeline connection, which resulting in reduced delivery efficiency and even failure to work properly.
When pipe blockage occurs, the pumping pressure increasing can be observed through the pressure gauge. While, slurry leakage often occurs at the pipe connection.
Main Causes Of Pipe Blockage And Leakage
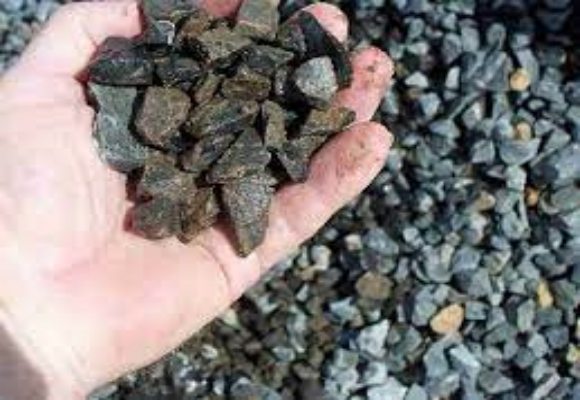
- Pump aggregate stones are too much. Segregation and other mix ratio does not meet the pumping requirements.

- External factors such as adding too much water (too high water/cement ratio) lead to concrete segregation.
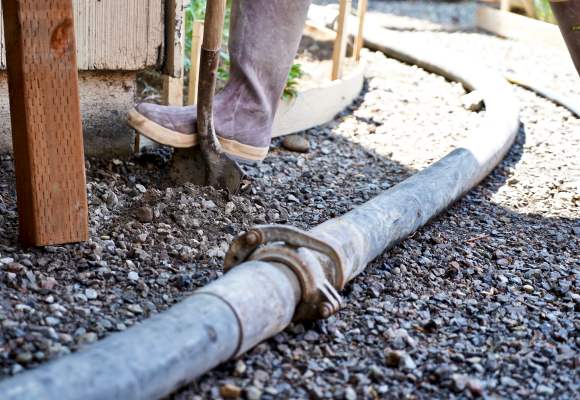
- Serious wear of sealing rings for pipe clamps lead to slurry leakage and pipe blockage as well as pump pipe falling off.
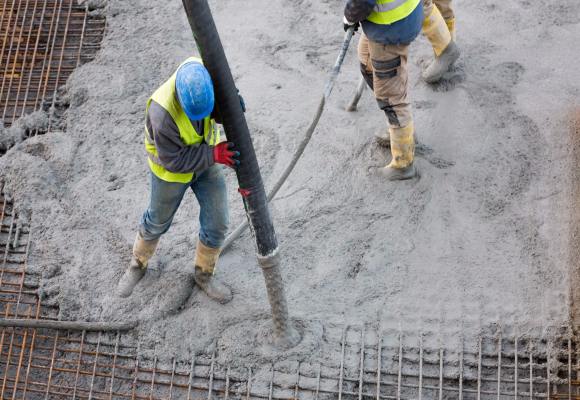
- The detachment of the steel wire layer of the hose, the severely worn concrete pipe, and the delamination of the double layer can cause pipe blockage and explosion
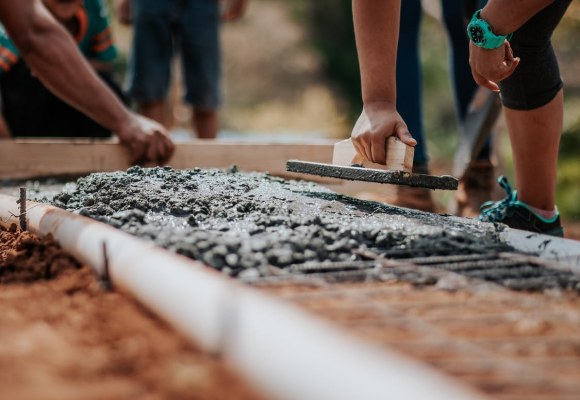
- Too much empty pumping, resulting in large concrete pipe pressure, causes the segregation of stone slurry.
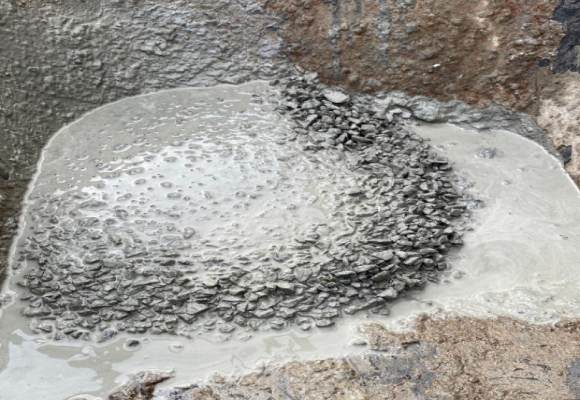
- When the waiting time is too long, the concrete in the pump pipe is not actively pumped.
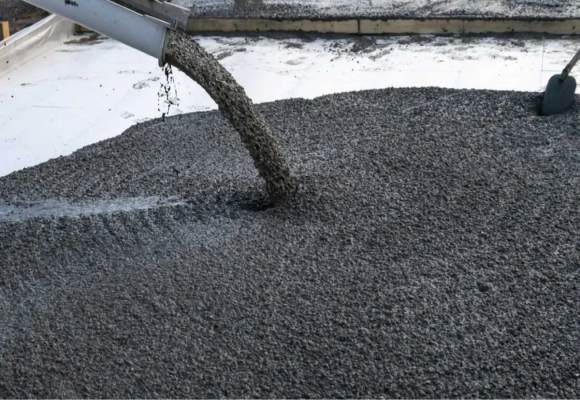
- At the beginning of pumping, too large displacement, untimely material discharge, and air into the pipe, result in pipe blockage.
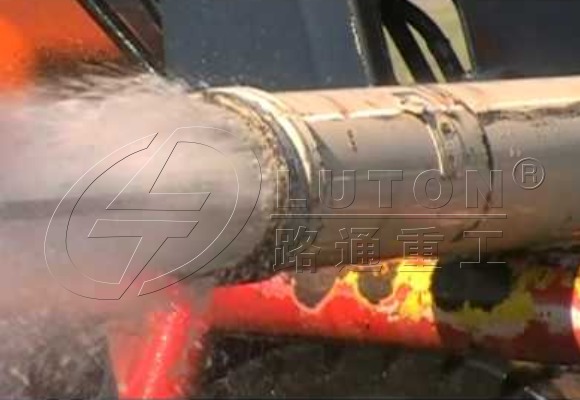
- Not cleaning pipeline after construction cause pipe blocking.
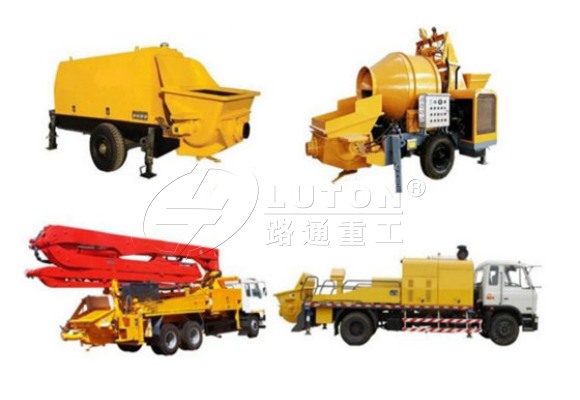
- Improper selection of the pumping equipment also may lead in pipe blockage.
Measures To Avoid Pipe Blockage And Leakage
To avoid concrete pump pipe blockage, the following measures are recommended to be taken:
- Adjust the concrete mix ratio reasonably to ensure the pumping requirements.
- Control the water supply and keep the slump of concrete within a reasonable range.
- Use well-graded aggregated and proportion concrete constituents properly
- Check the pump pipe and the sealing ring regularly, and replace the damaged parts in time.
- Reasonable control of the pumping speed and time, to avoid excessive empty pumping.
- Move the pump pipe in time while waiting for the concrete material to avoid by concrete solidification.
- Strictly follow the operating procedures to avoid the air into the pipeline caused by excessive discharge or delayed discharge.
- Check the wear condition of the hose steel wire layer and the concrete pipe regularly, and replace the damaged parts in time.
- Clean the pipe in time after construction to avoid pipe blockage caused by residues.
- When a pipe blockage occurs, try to reverse the pump and then continue the forward pumping. If the problem cannot be resolved, stop the machine immediately and remove the blockage to maintain the continuous transport of the concrete and prevent the mud agglomeration or precipitation in the pipe.
Insufficient Pumping Pressure Or No Pumping Pressure
In the pumping process, if the pressure is insufficient or zero, it will lead to unnormal concrete conveying. It will finally affect the construction progress.
Main Reasons For The Unnormal Pumping Pressure
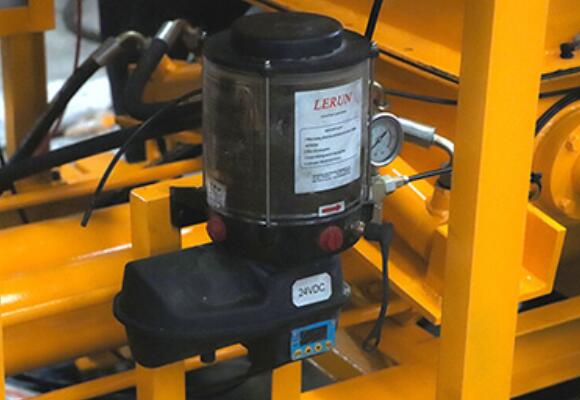
- Hydraulic Oil Insufficient
Hydraulic oil is the medium to drive the operation of the concrete pump. If the oil volume is insufficient, it will affect the normal operation of the pump, resulting in insufficient pressure or no pressure.
- Oil Circuit Is Not Smooth
If the hydraulic oil circuit is not smooth, it will lead to the oil can not flow smoothly, and result in insufficient pressure or no pressure.
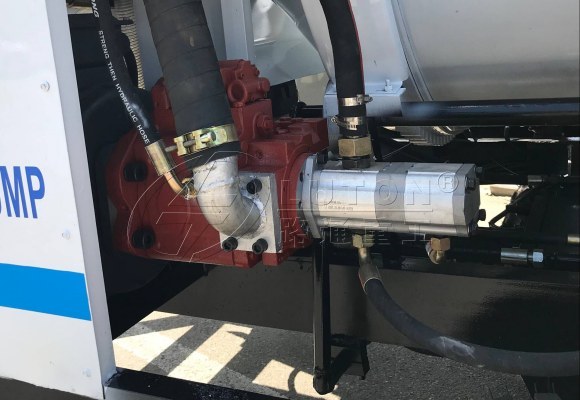
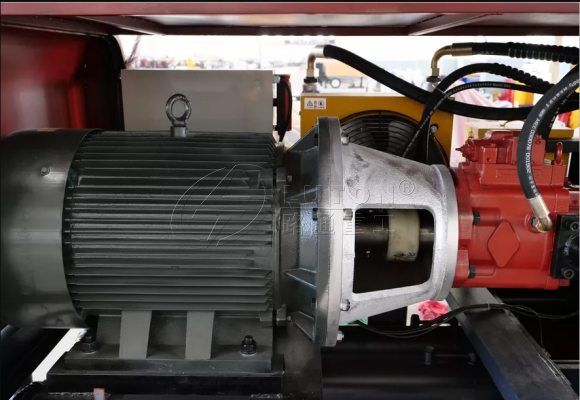
- Motor Fault
The motor is an important part to drive the operation of the concrete pump. If the motor fails, it will affect the normal operation of the pump, resulting in insufficient pressure or no pressure.
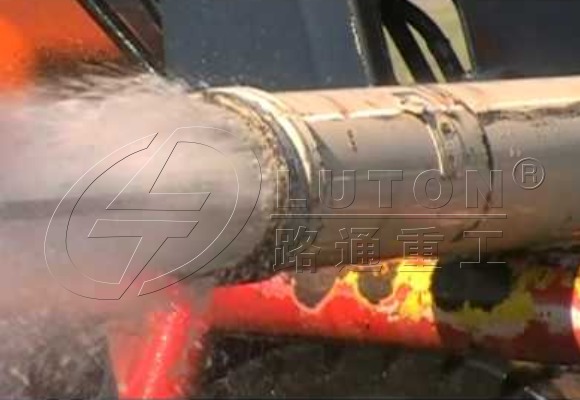
- Pipe Leakage
If the pipeline leaks, it will cause the concrete pump cannot work normally, thus affecting the normal operation of the pump, resulting in insufficient pressure or no pressure.
- Concrete Quality Problem
If there is a problem with the quality of the concrete, it will lead to the pumping is not smooth, thus affecting the normal operation of the pump, resulting in insufficient pressure or no pressure.
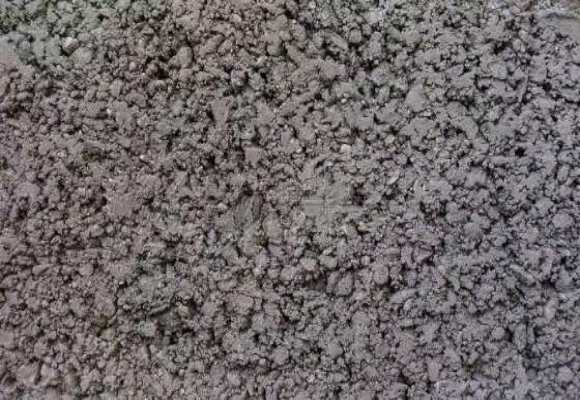
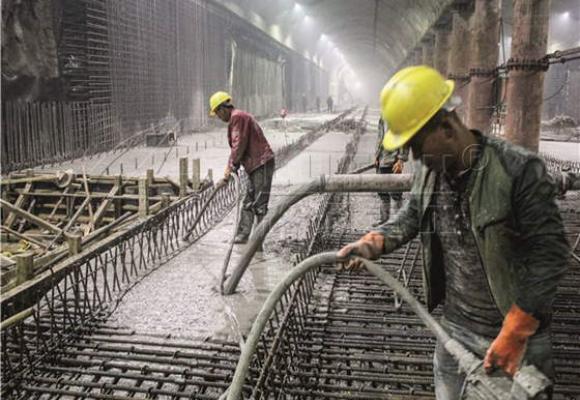
- Improper Operation
If improper operation, the concrete pump will be unable to operate normally, thus affecting the normally, thus affecting the normal use of the pump, resulting in insufficient pressure or no pressure.
Solutions Of Abnormal Pumping Pressure
To solve the problem of insufficient or no pressure of concrete pumping, the following measures are recommended as following:
- Check the oil quantity of hydraulic oil, if it is insufficient, add hydraulic oil in time.
- Inspect whether the oil circuit of the hydraulic oil is smooth. If not smooth, clear the oil circuit in time.
- Examine the motor working situation. If it is not normal, repair or replace the motor in time.
- Check the pipeline. If it leaks, replace the pipeline in time.
- Ensure the quality of concrete. If it does not meet the requirements, adjust the concrete mix ratio in time.
- Check the operation of the concrete pump. If it is not properly, correct the operation method in time.
Electrical Fault
The electrical part of the concrete pump may have various faults, such as motor damage, circuit failure, etc., resulting in the concrete pump can not work properly.
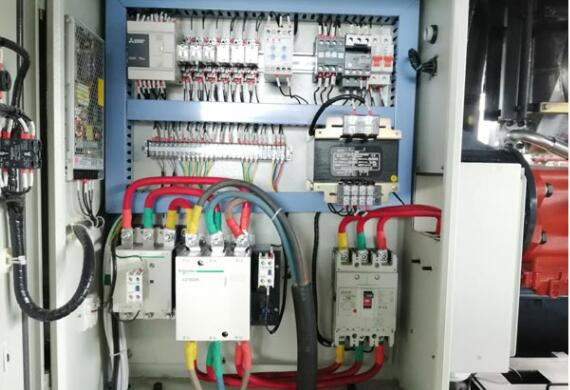
Reasons Of Electrical Faults In Concrete Pump
Concrete electrical failure may be caused by the following reasons:
- Abnormal voltage or phase loss: This may cause the thermal relay to trip, make the motor unable to start or make abnormal sound during startup. At this time, we should stop urgently and disconnect the power supply for inspection.
- Damage of certain components: For example, damage to spare parts such as thermal relay and intermediate relay may lead to circuit failure. That will need to be measured and replaced.
- Hydraulic system or motor failure may cause failure. For example, problems with hydraulic rod control, whether the overflow valve bolt is tightened, and whether the electromagnetic reversing valve is electrified.
Measures To Solve The Electrical Faults
- Measure the voltage, and check whether the supply voltage of the output power circuit breaker and the power grid power supply are normal.
- Replace problematic components, such as thermal relay, intermediate relay, etc.
- Check whether the hydraulic system and the motor are running normally, check whether the overflow valve bolts are tightened, and whether the electromagnetic reversing valve is electrified.
In general, the solution to the electrical failures need to be solved according to the specific problems.
Mechanical Breakdown
The mechanicla part of the concrete pump may appear wear, loose and other problems mainly due to long-term use or improper maintenance. These problems will affect the pumping effect.
The Main Causes Of The Concrete Pump Mechanical Failure
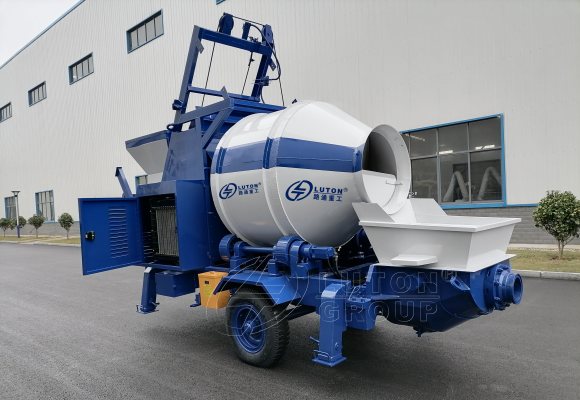
- Piston damage. The delivery cylinder damage is often the result of the function failure of the washing chamber caused by the entry of sand and concrete aggregate. And the hydrolysis of the piston at high temperature may lead to the piston damage.
- The lubrication of each part is inadequate. Due to the blockage of the lubrication points of various bearings and the mixing shaft sleeve, lubrications cannot performe properly.
- Spectacle plates and cutting rings are worn-out. Wear of spectacle plates and cutting rings of small agricultural concrete pumps is a common on-site phenomenon. S tube swinging improperly and rubber spring wear are the main reasons for increased wear.
- Abnormal operation of the gate valve. The lack of force and severe wear of the gate valve can lead to errors in its operation.
The Treatment To Concrete Mechanical Failures of Concrete Pumps
- Regular Maintenance: For concrete pump equipment, timely inspection and maintenance are very important. It can reduce the occurrence of faults and extend the service life of the equipment. Regular inspections can promptly identify and address issues, preventing small problems from becoming major ones.
- Professional training for operators: At the construction site, concrete pump operators must possess professional operating skills and safety knowledge. When using concrete pumps, it is necessary to operate according to the operating specifications to ensure the normal operation of the equipment.
- Replace aging equipment: Equipment aging is one of the main reasons for damage to concrete pumps. When the concrete pump equipment ages to a certain extent, it is necessary to replace the equipment in a timely manner or carry out major repairs. This will extend the service life of the equipment and reduce the failure rate.
In general, solving mechanical faults in concrete pumps requires corresponding solutions based on specific issues.
Hot Models Of LUTON Concrete Pumps
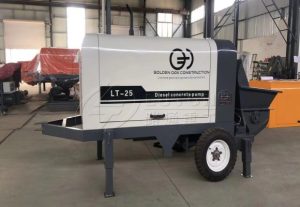
Mini Concrete Pump
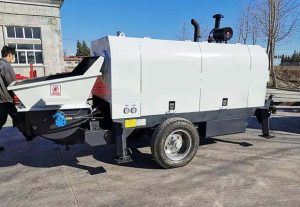
High-Pressure Concrete Pump
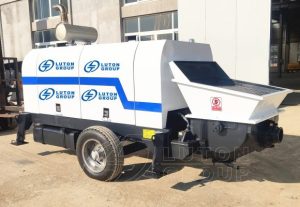
Concrete Trailer Pump
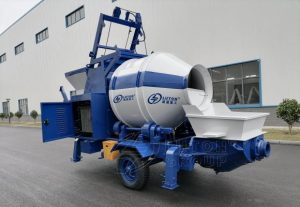
Concrete Mixer Pump
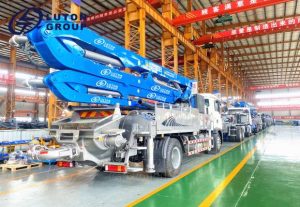
Concrete Boom Pump
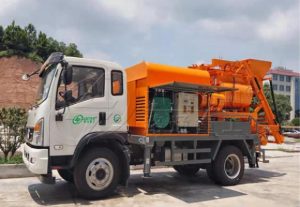