Concrete pump maintenance is an important guarantee for the efficient transportation of concree in modern construction. As an indispensable core equipment in modern engineering construction, concrete pumps performance directly affect the progess, quality and cost of the whole project.
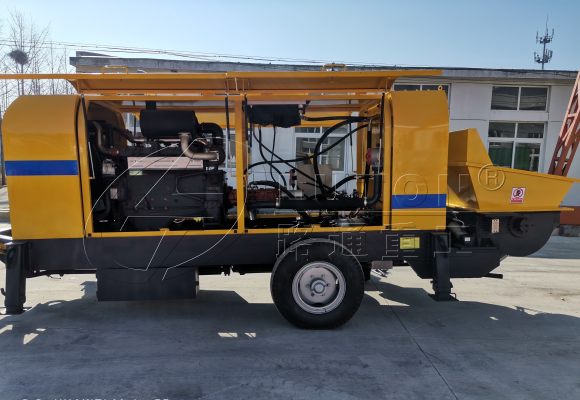
However, without scientific and standardized maintenance work, enven the highest quality concrete pumping equipment will gradually experience frequent malfunctions. Such as wear, leakage, blockage, even a sharply reduced lifespan. Therefore, it is particularly important to master scientific maintenance knowledge and skills. So how exactly should concrete pumps be maintained? Please refer to the maintenance reference provided by LUTON GROUP for you.
General Maintenance For Concrete Pump Equipment
Daily Maintenance
Daily maintenance is the foundation of the maintenance of concrete pump equipment. The maintenance content after daily use includes various aspects, such as the appearance inspection of the pump body, oil level check, inspection of composition of each major system, as well as necessary cleaning, to ensure that each component system can operate normally.
First of all, after each use, the pump body and the conveying pipeline should be cleaned. Make sure there is no concrete residue.
Then, check whether there is any loosening or abnormal wear in each part of the pump body. And correct or replace it in time.
Also, it is necessary to inspect and maintain the main component systems of the pump machine.
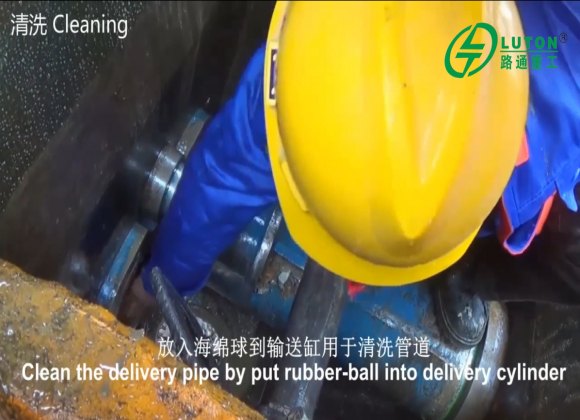
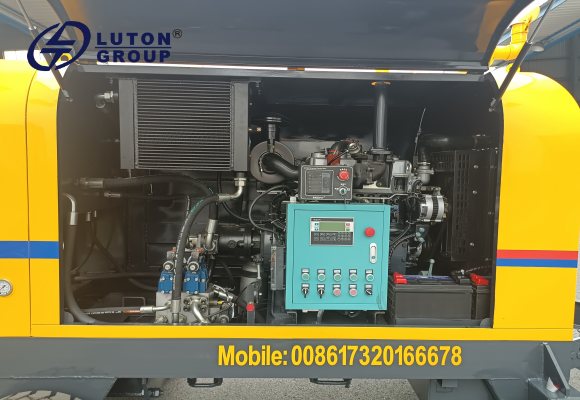
Maintenance Of The Lubrication System
Regarding the maintenance of the lubrication system, there are some tips as following:
First of all, check the lubrication points.
- Check the lubrication points of key parts, such as the swing shaft of the S-tube valve, the bearings of the mixing shaft, and the piston rod. Ensure that the grease at each lubrication point is fully visible.
- If there is any underlubrication, it should be replenished in time with high-temperature resistant lithium-based grease.
Second, check the automatic lubricate system.
- Check the actual oil storage volume of the automatic lubrication system, which should be greater than 80% of the total oil storage volume.
- Note that lubricating grease needs to be replenished for every 200 cubic meters of concrete pumped.
- During the process of adding grease, it is important to note that the interval between grease injections should be controlled at 15 to 20 minutes per time.
Inspection And Maintenance Of Hydraulic Systems
There are also two main tips on hydraulic systems care.
Oil Level Check
- Make sure that the oil level in the hydraulic oil tank is controlled at a level above two-thirds of the volume range the window showed.
- During the operation of the pump, the hydraulic oil temperature should also be monitored in real time. The temperature should be between 30โ and 60โ. If it exceeds 70โ, the machine should be stopped immediately to check the cause of overheating.
Filter Element Inspection
The clogging condition of the return-oil filter elemeter should be checked daily.
- When the pressure difference is greater than 3bar, the filter element needs to be replaced.
- Check the cleanliness of the oil. The oil liquid should be clear and transparent, without obvious turbidity or discoloration ( for example, new oil is generally light yellow or transparent).
Inspection Of Pumping System
- Check the pumping system free of blockage and leakage.
- Check the pumping pipeline without severely worn.
- If there are problems of the above two situation, treat them and replace relevant parts in time.
Regular Maintenance Of Concrete Pump
Based on the type of concrete pumped, usage frequency and environmental conditions, a reasonable replacement cycle for vulnerable parts should be formulated. Generally, it is recommended to conduct a comprehensive inspection every 300 hours to 500 hours of pumping work, or do it once a month. And replace the vulnerable parts according to the inspection results.
Weekly Maintenance
Deep Cleaning
- Thoroughly clean the residue in the concrete hopper with a high-pressure water gun, paying specail attention to the accumulation of materials at the bottom of the mixing blades.
- Clean the vulnerable parts and their surronding environment every week to prevent concrete residue and dust accumulation from causing accelerated wear. At the same time, regularly lubricate the components that need lubrication, such as pistons, conveying cylinders, etc.
Check The Wear Condition Of Vulnerable Parts
- Ensure the wear of the mixing blades. When the wear at the blades top exceeds 15mm, it should be repaired by surfacing welding.
- Measure the gap between the spectacle plate and the cutting ring. When adjusting the gap, follow the manufacturer’s recommended value ( for example, the standard gap is 0.1-0.3mm. And it needs to be adjusted if it exceeds 0.5mm) to avoid excessive tightness or looseness, which may cause accelerated wear.
Electric System Inspection
- Test the insulation resistance of the motor using a megohmmeter. The normal situation is more than 5Mฮฉ(500V DC).
- Check the wiring terminals of the control cabinet. Ensure that each terminal is firmly and reliably connected.
Monthly Maintenance
Deep Maintenance Of The Hydraulic System
- Replace the hydraulic oil filter element (accuracy ฮฒโฅ200, filtration efficiency โฅ99.5%)
- Test the pressure of the main pump: The setting pressure error of the constant pressure pump is โคยฑ2%
Inspection Of Structural Components
- Ultrasonic flaw detection for key welds (such as hopper supports, S-pipe supports)
- Bolt tightening: Tighten in a diagonal sequence
Seasonal Maintenance
Maintenance In Winter
In cold seasons, it is necessary to ensure that the temperature of the pumping system is appropriate to prevent equipment damage caused by low temperatures.
Add antifreeze to prevent the pipes from cracking due to freezing.
Maintenance In Summer
During the hot season, the maintenance of the heat dissipation system should be strengthened to ensure that the pumping system does not malfunction due to overheating.
Annual Maintenance
Power System Renovation
- Diesel engine: Replace the timing belt (mandatory replacement after 2000 hours of operation)
- Motor: Bearing replacement (Immediate handling is required when vibration value > 4.5mm/s)
Detection Of Hydraulic Components
- The volumetric efficiency test of the plunger pump shows that if it is lower than 85%, maintenance or replacement is required
- Hydraulic cylinder internal leakage detection: When the piston rod is extended, the settlement within 5 minutes is โค5mm
Other Precautions
Professional Operation
The maintenance work of mechanical systems should be carried out by personnel who have received professional training to avoid blind operation by non-professionals, which may cause equipment damage or personnel injury.
Recording And Tracking
After each maintenance, detailed records should be made of the maintenance content, time, replaced parts and other information to facilitate subsequent tracking and analysis.
Respond Promptly
When any abnormality or malfunction of the mechanical system is detected, the machine should be stopped immediately for inspection to prevent minor issues from escalating into major ones and causing greater losses.
Preventive Maintenance
Regular preventive maintenance should be carried out, such as checking the wear of mechanical parts and the loosening of fasteners, to identify and solve problems in advance.